Electrode Storage and Drying
- interweldweb
- Dec 6, 2021
- 3 min read
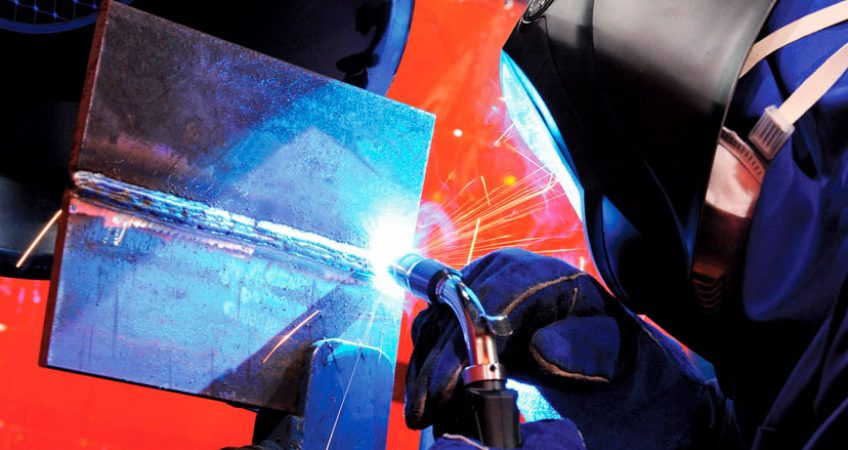
1. Introduction Shielded metal arc welding (SMAW) electrodes or stick electrodes must be stored properly to deposit quality welds. When rod electrodes absorb moisture from the atmosphere, they must be dried to restore their ability to deposit quality welds. Electrodes with too much moisture can cause cracks or porosity. Operational characteristics can also be affected. If you have experienced unexplained weld cracking problems, or if the arc performance of the stick electrode has deteriorated, it may be due to your storage methods or drying procedures. Follow these simple storage, exposure, and drying techniques to ensure the highest quality welds as well as the best operating characteristics for your stick electrodes.
2. Storage of low hydrogen stick electrodes. Low hydrogen stick electrodes must be dry to function properly. Unopened Lincoln hermetically sealed containers provide excellent protection in good storage conditions. Opened cans should be stored in a cabinet at a temperature of 250 to 300 ° F (120 to 150 ° C). Low hydrogen rod electrode coatings that have absorbed moisture can cause hydrogen induced cracking, particularly on steels with a yield strength of 80,000 psi (550 MPa) and higher. Moisture resistant electrodes with an "R" suffix in their AWS classification have a high resistance to moisture wicking coating and, if stored properly, will be less susceptible to this problem, regardless of the yield strength of the steel being welded. Specific code requirements may indicate exposure limits other than these guidelines. All low hydrogen stick electrodes must be stored properly, even those with an "R" suffix. Standard EXX18 electrodes must be supplied to welders twice per shift. Moisture resistant types can be exposed for up to 9 hours. When containers are punctured or opened, low-hydrogen electrodes can accumulate moisture. Depending on the amount of moisture, it will damage the quality of the weld in the following ways: a) More moisture on low hydrogen electrodes can cause porosity. Detection of this condition requires X-ray inspection or destructive testing. If the base metal or weld metal exceeds the yield strength of 80,000 psi (550 MPa), this moisture can contribute to bead or weld cracking. b) A relatively high amount of moisture on low hydrogen electrodes causes visible external porosity in addition to internal porosity. It can also cause excessive slag flow, rough weld surface, difficult slag removal, and cracking. c) Strong moisture absorption can cause weld cracks in addition to under-bead cracks, severe porosity, poor appearance, and slag problems.
4. Re-drying conditions: low hydrogen stick electrodes
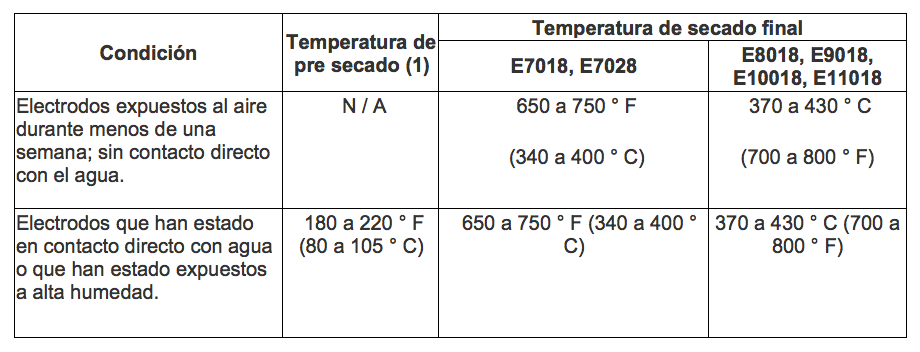
(1) Pre-dry for 1 to 2 hours. This will minimize the tendency for coating cracks or for oxidation of the alloys in the coating to occur.
1. Storage and drying of electrodes that are not low hydrogen content Electrodes in unopened Lincoln cans or boxes retain proper moisture content indefinitely when stored in good condition. If exposed to humid air for long periods of time, the contact electrodes of open containers can absorb enough moisture to affect the performance characteristics or the quality of the weld. If humidity appears to be a problem, store electrodes from open containers in heated cabinets at 100 to 120 ° F (40 to 50 ° C). DO NOT use higher temperatures, particularly for "Fast Freeze" group electrodes. Some electrodes from damp containers or from prolonged exposure to high humidity can dry out again. Follow the procedures in the following table for each type. 2. Re-drying conditions: stick electrodes that are not low hydrogen content.

Comentarios